Retired Wind Turbine Blades (Fiberglass Products) Resource Utilization Disposal System
Scope of Application:
Wind turbine blades
Glass fiber
Blade leftover
Glass products
Online Inquiry
Wind turbine blades
Glass fiber
Blade leftover
Glass products
Description
Wind energy is a renewable, inexhaustible, and clean energy source. Now wind energy is mainly used for power generation and has achieved large-scale development and application globally. In order to meet the growing demand for installed capacity, the size, strength, and weight of wind turbine blades (one of the core components of wind turbines) are also continuing to increase. In previous production, wind turbine blades are made of thermosetting resin based composite materials reinforced with glass fiber (GF), carbon fiber (CF), or GF/CF mixture with high pan stress. Retired wind turbine blades (fiberglass) are difficult to recover through traditional treatment methods. Currently, common resource utilization technologies for wind turbine blades can be divided into five categories: disassembly and reuse, cement kiln collaborative disposal, hot melting, pyrolysis, and solvent decomposition.
SOYU Machinery provides a professional resource disposal system for retired wind turbine blades, with a maximum production capacity of 10 tons/hour, exploring a feasible and cost-effective technical approach for batch harmless disposal of retired wind turbine blades.
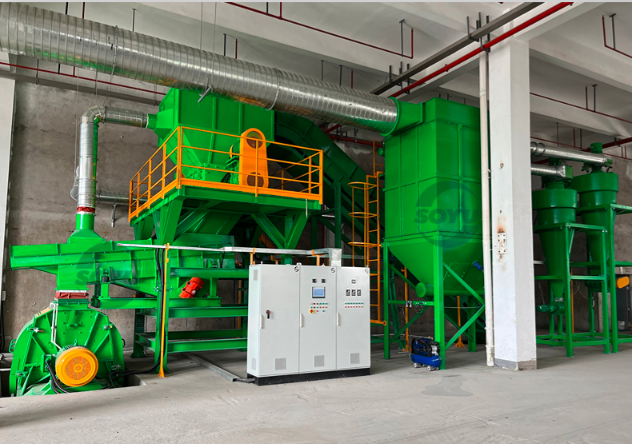
SOYU Machinery provides a professional resource disposal system for retired wind turbine blades, with a maximum production capacity of 10 tons/hour, exploring a feasible and cost-effective technical approach for batch harmless disposal of retired wind turbine blades.
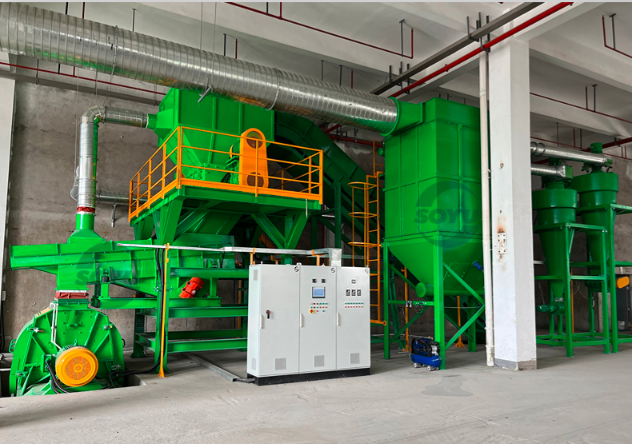
Product structure
-
- 1,Shredder
Special shear structure optimization, low speed and high torque enable the equipment to adapt to different working conditions. The cutting blades are made of imported wear-resistant materials, with excellent wear resistance, which have longer service life. Optional surfacing repair process to reduce blade usage costs.
- 2,Control system
The Intelligent automation control system centrally controls each production unit of the entire line, including functions such as one click start-stop, status monitoring, data analysis, fault diagnosis, personalized data reporting, and alarm linkage. The key equipment of the entire line is equipped with intelligent sensing devices, which can monitor operating data in real-time and provide real-time feedback to the control system. Personalized data reports help operators comprehensively understand the operational status of production systems and achieve intelligent management.
- 3,Powder collection system
The material enters the conveying pipeline through the feeding device, is mixed with high-speed pneumatic force, and then transported to the end receiving silo. The fitered gas is discharged into the atmosphere through the material gas separation device. The conveying process is fully sealed, effectively avoiding dust issues.
- 4,Air gravity sorting system
Materials fall along a special structural pipeline under the action of gravity, and are screened by the difference in buoyancy and gravity of the airflow. The multi-layer separation structure ensures the sorting effect, occupies a small area, and has low operating and maintenance cost
- 5,Fine crusher
Materials are crushed and ground by high-speed rotating shaft hammering to obtain refined materials.
- 6,Grinding unit
Full automation, automatic feeding, discharge, screening;
The grinding process is completely sealed, without dust leakage;
Adjustment of grinding gap, powder size 10~120 mesh adjustable;
Adopting a combination of air and water cooling system to effectively control the internal working temperature of the grinding chamber and prevent thermal plasticization of the grinding materiall
- 7,Dust removal system
The pulse dust removal system automatically collects the dust generated during crushing and uses the filtering effect of fiber fabrics to filter the dusty gas, improving the cleanliness of the site.
- 1,Shredder
-
Rendering after crushing
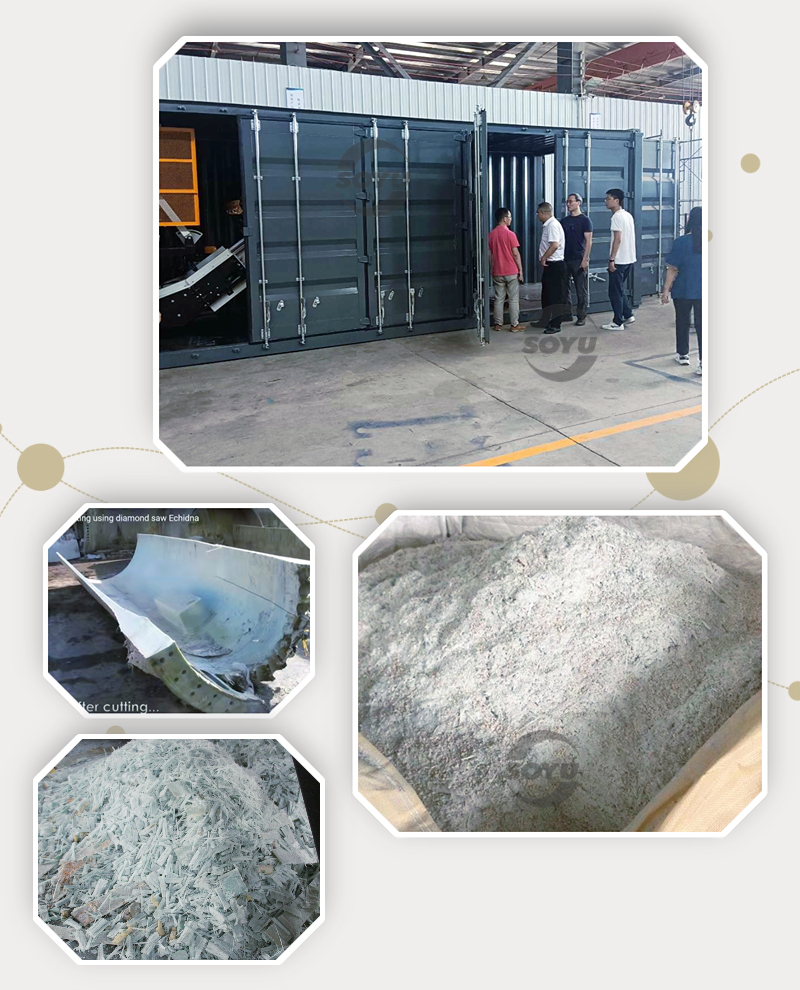
Cases
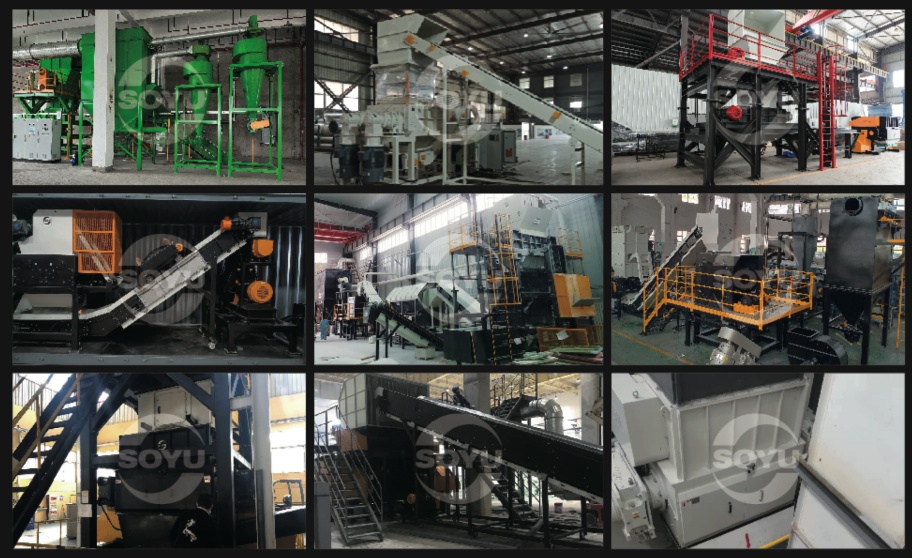